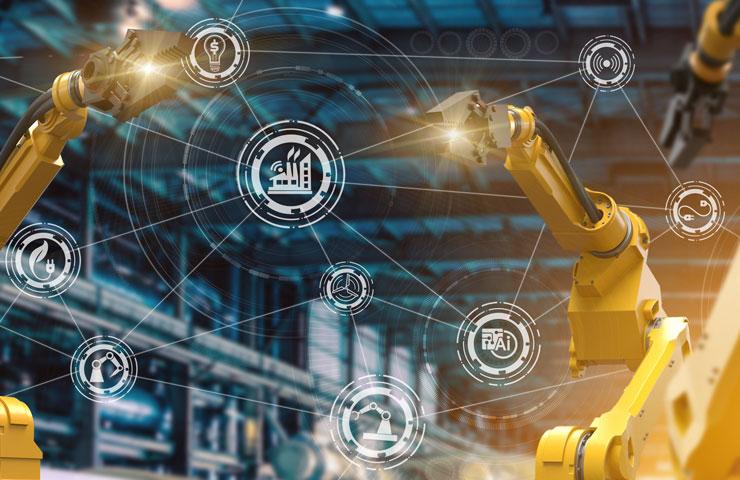
Internet of Things (IoT) offers significant advantages in terms of efficiency and costs. Connectivity, mobile solutions and sensor technology not only simplify operational and maintenance processes but can also be used to push these to the next level.
With “Azure”, Microsoft offers a cloud platform and technology which allows you to easily develop apps. The use of mobile apps allows important information to be made available directly on mobile devices such as smartphones or tablets while maintaining high security standards.
Newly developed sensors for technical objects such as pipes, motors and pumps provide essential data which allows for a whole range of optimizations. Using IoT is worthwhile in safety- and logistics-relevant applications, as well as for predictive maintenance. In the following, several examples are given of how you can benefit from the use of IoT in your production or maintenance operations.
Example 1: Leak monitoring of critical piping elements
Characteristic sensitive points such as flange connections or transitions on vessels are continuously monitored by high-performance, durable sensor units. Instead of having inspection teams working on site, sensors are used to measure leakages, where applicable – thus saving you trips and time!
Example 2: Predictive maintenance
Intelligent sensors are capable of capturing data from many locations, e.g. on pumps or compressors, which are then evaluated and used to provide information on when certain components in production need to be repaired or replaced. Automatic evaluation of data for the optimization of maintenance cycles results in predictive maintenance.
Example 3: Identification of deviations in daily operation
Sensor-based data on machines, systems or the equipment is analyzed on the basis of artificial intelligence. As soon as there is a deviation from the normal state, a service ticket is automatically created to investigate the corresponding irregularity and prevent further problems from arising.
Example 4: Simple ways to increase system efficiency
In piece goods manufacturing, short interruptions often occur between the manufacturing and the final packaging stage. Since such interruptions only last several seconds, they are often disregarded when assessing plant efficiency. With simple sensor technology, these micro-stops can be systematically recorded and accumulated. The overall extended downtime period prompts a closer examination of the causes, the elimination of which can significantly improve the efficiency of the entire plant.
Example 5: System efficiency
With regards to products that are identical or similar in terms of manufacturing using (almost) identical equipment, it is reasonable to compare the factors availability, quality, and productivity. The results can be used to draw conclusions about the machine (condition), the type of operation (shift type and qualification) and other efficiency-related criteria.
Example 6: Detection of sporadic errors
There is indeed no sensor that is capable of detecting sporadic faults. However, with the help of a sensor system – in combination with camera technology – this type of defect can often be eliminated. The investment is admittedly high, but, on the other hand, puts an immediate end to cost-intensive recalls, complaints, etc.
How do you plan to profitably establish IoT in your company?
Are you well positioned in all phases of digitization or do you still see a need for optimization? Why not talk to one of our seasoned industry management consultants?
Keywords
More similar blogposts:
Found what you were looking for?
Start your intelligent search now