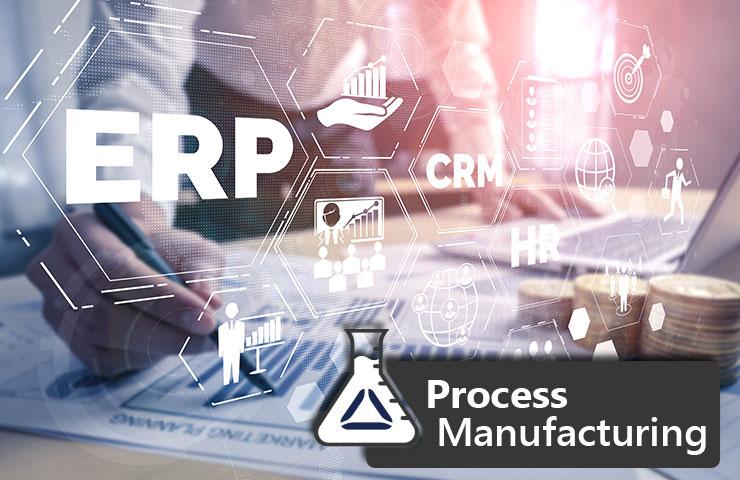
Why is ERP system modernization so important for process manufacture in particular?
30% Increase in Value Added in Only 4 Years
The German Chemical Industry Association predicts that the process industry is planning to invest more than €1 billion in digitalization projects and new sustainable business models over the next few years. After all, organizations that successfully collect and analyze their data along the entire value chain secure a huge competitive advantage. And a study by the Fraunhofer Institute research organization suggests that a digital approach to the product life cycle in the process industry could lead to a 30% increase in value creation by 2025. This forecast alone is reason enough to address this issue.
The Key to Successful Digitalization
The key to successful digitalization is to involve all employees. Managers should therefore provide transparent and frequent information about planned changes and progress. After all, digitalization not only moves the company forward, but everyone involved benefits from the multitude of innovations.
What Can I Contribute as a Supplier to My Customer’s Success?
This aspect needs to be combined with the opportunities offered by digitalization and data-driven business models being realized. After all, digitalization primarily involves collecting and evaluating data, i.e. assigning and archiving receipts, emails, invoices and other business documents in the ERP system. This accelerates and simplifies business processes.
ERP also becomes an issue when it comes to connecting customers, employees and suppliers via a web browser. The web portal as an integral part of the ERP system can be implemented efficiently and independently of platform, device and location. Each authorized user accesses their data online in real time and receives everything they need customized to enable them to complete their tasks.
How Can I Optimize My Supply Chain?
Digitalization opens up opportunities for chemical companies to optimize their supply chains. In the context of increasing networking and digitalization, the focus is shifting more and more towards process knowledge and innovative IT solutions. The key to all this is open and flexible platforms. Data from sensors or system controls can be used to accelerate decision-making processes without jeopardizing ongoing production. The transparency this creates optimizes the plant’s daily workflow.
Another example is monitoring process data and the resulting analysis of anomalies. This means failures can be predicted to reduce unplanned downtime and improve overall equipment effectiveness (OEE), which very quickly reduces maintenance costs. The quality assurance process improves the analysis of quality-relevant data and better results in terms of quality ultimately also generates higher customer satisfaction.
How Do I Get All Data into a Standardized Form?
This question fundamentally refers to transformation: from document management to data-driven information management.
Production processes are not only being digitalized; they are also becoming more flexible as a result of seamless networking. Real-time transmission of all data, for example, not only gains an insight into capacity utilization and a plant’s current order book, but the order sequence can also be changed at short notice. This means production can be designed more flexibly and directly respond to current demands.
Tip: How to Get Started
Artificial intelligence is a great example of using data-driven information management. Using small and lean solutions, you can already analyze product delivery periods in a variety of ways. Artificial intelligence detects deviations from the norm, factors in various influences and makes recommendations for optimum replenishment lead times. If you regularly carry out this analysis, you automatically improve data quality and delivery.
Incidentally, our examples are hybrid approaches. While they do both utilize the cloud, they do not require the ERP system itself to be run in the cloud. Current ERP solutions, such as Microsoft Dynamics 365 products, can easily cope with these requirements. At the same time, you also get a wide enough range of functions to handle the special requirements of process manufacturing.
And then it continues:
- What could the initial project look like?
- What needs to be considered?
- Which technologies are needed?
- What impact will this have on the company?
- How can the different applications be linked together?
Each step gives you deeper insight into the technologies ready for you to take the plunge into the next step. There’s no need to put all your eggs in one basket. You can still run your company systems on-premises and simply add cloud functions on to them as needed. In any case, large, rigid and monolithic systems are on their way out. A modern business solution needs to be flexible, as well as open to new technologies, concepts and ideas.
At COSMO CONSULT, digitalization means:
- simplifying things (make them more accessible)
- realizing things reliably (to make them predictable)
- changing things (to transform innovatively)
- optimizing things (to make them better)
- approaching things in an agile way (planning in portioned steps)
- solving things intelligently (to make things smarter)
Keywords
More similar blogposts:
Found what you were looking for?
Start your intelligent search now