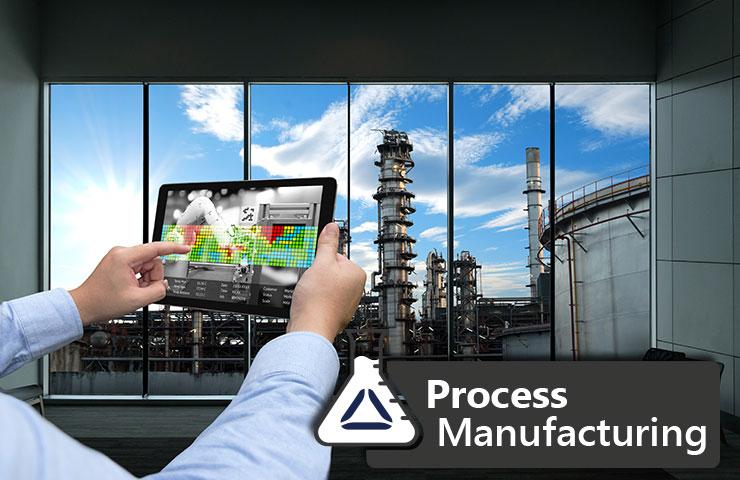
The Internet of Things (IoT) offers mid-sized companies significant advantages in terms of efficiency and costs. Connectivity, mobile solutions and sensors simplify operation and maintenance.
All of this is based on the groundbreaking innovations of the past few years - cloud computing, big data analytics, edge computing and cheaper, much more diverse sensor technology.
What’s more, with “Azure", Microsoft offers a cloud platform and technology which allows you to easily develop apps. These applications can simply be integrated into the Microsoft environment.
The use of mobile apps significantly improves interaction when it comes to process coordination. Important information is directly accessible on mobile end devices (such as smartphones or tablets), and security standards are high.
New sensors for new business models
Newly developed sensors for technical objects such as pipes, motors, and pumps provide essential data which allows for a whole range of optimizations, whether it be related to security, service life, logistics, or predictive maintenance.
In the Internet of Things, Edge Computing is becoming more and more important. A variety of more and more affordable end point sensors provide critical measurement data, for example relating to temperature or leakages. Since mobile radiocommunications would be a bit “over the top” and too expensive in these scenarios (each sensor would need to have its own SIM card), so-called “Low Power Wide Area Networks” come into play, such as LoRa and Sigfox or Mioty, which has been developed by the Frauenhofer Institute.
Maintenance on a new level
An important goal is to push maintenance to the next level.
You can ease the workload of your maintenance team by using sensors that automatically transfer measurement data to the cloud - data which is then analyzed for predictive maintenance and digital inspection. The majority of the expenses for compliance with the regulations can be saved by means of digital processes. It’s not just large corporations that benefit from these digital solutions, but also mid-sized companies operating small machines.
Tracking via sensors that gather life-cycle data also plays an important role - not only for operations but also for logistics and assembly.
Evaluating this data is absolutely vital for predictive maintenance, as the following examples illustrate:
- Safeguarding important assets against failure and being able to determine the probability of failure
- Condition monitoring (continuous monitoring of the condition of components, e.g. temperature, wall thickness)
- Meeting regulatory requirements (e.g. tightness of the flange connections)
- Reducing the amount of unproductive work (searching, checking, visual inspections ....)
Keywords
More similar blogposts:
Found what you were looking for?
Start your intelligent search now