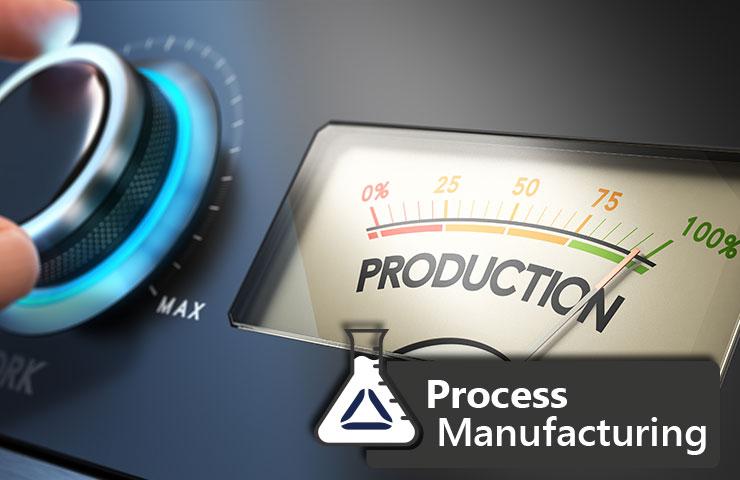
Delivering on time & remaining within your budget
On-time delivery to the customer is what most manufacturers consider their main challenge when it comes to batch production. Materials planning is a highly complex task given the need to meet delivery deadlines. Essentially, materials planning refers to a company’s coordination of resources within batch production. The goal is to meet the complex requirements despite a limited amount of resources. This does not mean fully meeting every single requirement, though. In many small and mid-sized companies, the materials requirement planner takes on responsibility for the coordination of resources in order to meet the agreed deadlines. Ideally, the ERP system makes use of the master demand schedule and calculates what is needed when by means of material requirements planning (MRP).
What will batch production look like in the future?
In the future, batch production will be characterized by collaborative materials planning. This kind of materials planning is based on a consistent data model through networked applications. Effective, collaborative materials planning compiles data from a variety of sources and makes it accessible in a format that allows for quick decision-making. In order for that to function, many components must be available. This includes traditional data collection and processing. Examples for this are production data acquisition, machine data acquisition, quality data acquisition and the collection of logistical data (traceability), but also further processes that have an immediate impact on the production process. Information must be broken down to the essential pieces so that the facts for the analysis can be presented effectively and in the right context. Actions or downtimes should trigger predefined workflows. The advantages of such a scenario are agility in terms of organization and predictability. This leads to improved profitability, since decisions are made based on a single, reliable base of information with actual business factors.
Keywords
More similar blogposts:
Found what you were looking for?
Start your intelligent search now