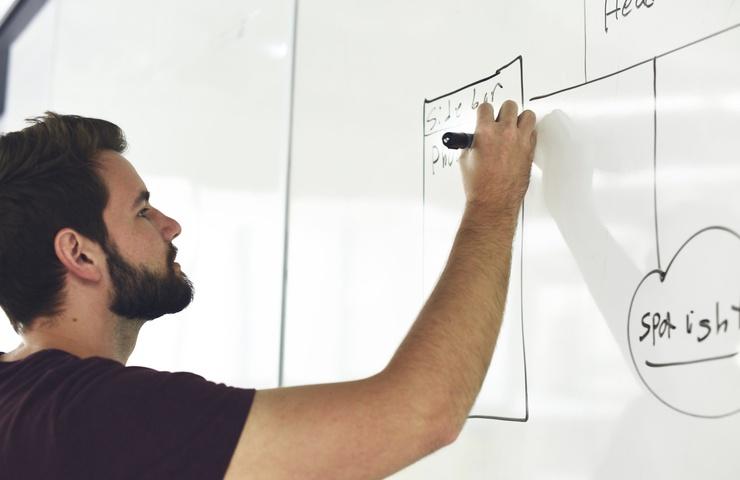
Manufacturing requirements change all the time. Lots become smaller and smaller, deadlines become tighter and quality requirements keep on increasing. This leads to new challenges for the various specialist departments which usually converge centrally in the planning department.
Ultimately, the planner needs to master the task of having the right quantity of the right product ready for delivery at the right due date. He is confronted with various problems and has to make the right decision many times a day.
Challenges and questions in flexible planning
The question as to whether a quantity split could be sensible arises if customers order larger quantities, yet require – i.e. call off – only partial quantities per day or week. When should which (partial) quantity be ideally manufactured?
External manufacturing describes outsourcing those processes which cannot be performed in-house either for reasons of capacity or technology. What is manufactured where, and who has available capacities?
The planner also considers the availability of purchased parts and raw materials. When do I have which quantities available? How do I make sure that I have the required materials available at the right time? How do I handle shortages and conflicts? What can be used as an alternative material?
Ideal resource utilisation is crucial as well. How can I utilise my resources in the best possible way? At which point do I have to schedule gaps to allow for manufacturing urgent subsequent deliveries or unplanned top priority orders?
Unpopular idle times must also be considered. How do I handle planned and unplanned maintenance? What time buffer do I have to include? Which efficiency rate can I expect?
Reserved capacities are scheduled for orders without the necessary details. Customers order quantities of product groups, but the details of the product (colours, types, etc.) are yet to be specified. These details (product specifics or also quantity structures) are announced at short notice. How do I account for this foresightedly?
The answer is in the details
To overcome these challenges and have the right answers to the above questions, planners need a maximum of flexibility when planning resources. A good planning system must assist them in all of their decisions with the proper information and the correct functions.
There is a variety of information or data planners should have available to this end which can differ depending on company and manufacturing process.
- Details regarding products, routes and bills of material,
- details regarding design such as colour sequence, special colours (not in stock) and coverage,
- details regarding raw materials such as grammage, wait times and fibre orientation,
- details regarding customers, delivery dates and call-off dates,
- details regarding required special equipment and tools such as grippers, printing cylinders or cutting die numbers,
- information regarding the status of the order or the processes such as progress or already manufactured quantities,
- document attachments such as layout drawings, product specification and product image,
- indicators as warnings in case of conflicts, e.g., in case of delivery date difficulties, overlaps, material and tool availability.
On the one hand, the planner requires a variety of data and information to make the best job possible and find the ideal planning sequence. On the other hand, a sustainable system must assist him with a range of functions allowing him to efficiently transform the requirements imposed and information provided into the best-possible results.
The following functionalities serve as helpful support in practice:
- Moving and/or merging one or several orders: due to the continuous change in the planning sequence, rearrangements must work quickly and efficiently.
- Freeze period: although the planning sequence is subject to continuous change, it must be possible to define a period during which a planned operation is set and no changes are admissible.
- Change of resources: a process shall be manufactured on an alternative resource or, as the case may be, externally.
- Release: when an order (or a process) is handed over to manufacturing (shop floor control) for execution after final planning.
- Clip: when different processes or orders should implicitly be manufactured together in a block (e.g., same tools, same colour sequence, customer priorities, etc.).
- Simulations: if several planning options shall be developed and saved. Eventually, after evaluating the different options, a simulation is used for actual planning and the rest is discarded.
Conclusion
At the end of the day, there is much to gain or lose in planning. Right sequencing and early identification of possible conflicts can help utilise optimisation potentials leading to cost reduction and time saving. A modern planning system must assist the planner in every aspect to allow successful tapping of these potentials.
Keywords
More similar blogposts:
Found what you were looking for?
Start your intelligent search now