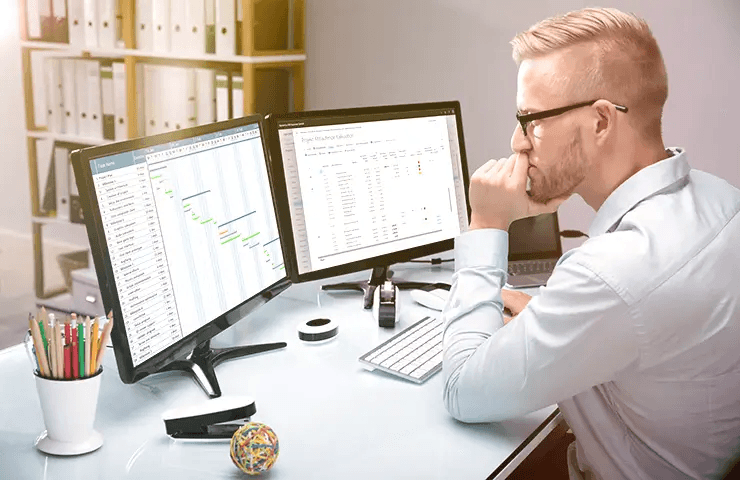
Interdepartmental, integrated costing ("concurrent calculation") has always been an issue in machinery and plant construction. How has this issue been around for so long, and why does it keep coming back on the agenda?
Machinery and Plant Construction is a Special Challenge...
...because you're normally dealing with a plethora of product variations and a high proportion of items specially developed for the order. Naturally, this makes costing more complicated and time-consuming. There are no fixed product structures that would allow us to pre-estimate the costs of an order or a project based on pre-defined BOMs and work plans.
What’s more, the sales costing breakdown is often different from the BOM breakdown that comes later – in Sales, they often work with estimates. Finally, as if that weren't enough, the products are also constantly changing between the quotation, the order, the design phase, and the production phase. Of course, this also needs to be reflected in the cost calculation in order to ensure reliable cost control.
Costing in discrete manufacture
“Fine, We’ve Got Excel for That!”
Since many ERP systems are poorly equipped to handle this kind of preliminary costing, people reach for other tools. The go-to choice here is Microsoft Excel. The problem with that? All that makes it into the ERP system is the order value. So the ERP system won’t be able to answer key questions like:
-
Was the sales estimate wrong, or was the order processing too complicated?
-
What is the current foreseeable profit margin?
Costing Does a Balancing Act
Machinery and plant construction businesses have very complex costing requirements. The keyword here is: flexibility. A modern simultaneous costing system has to do a balancing act between Sales and Product Development on the one hand and Engineering, Merchandise Management, and Production on the other.
Once a product is finally shipped and installed at the customer’s facility, all the associated costing data has to be submitted to the Cost Accounting Department. And that needs to include service and warranty expenses, in order to keep track of the entire product life cycle.
Conclusion
How can you tell a good industry solution for machinery and plant construction? Easy – by its simultaneous costing capability! It needs to offer flexible costing sheets that can be combined with equally flexible sales, order, and engineering BOMs from Production and Cost Accounting. This is crucial in order for your software to perform accurate preliminary costing. It’s crucial in order to obtain any reliable information on budget deviations. And it’s the only way your project leader can take action in time to complete all your orders at a profit.
How does your business handle simultaneous costing?
Be honest now... Do you still rely on Excel at all?
More similar blogposts:
Found what you were looking for?
Start your intelligent search now