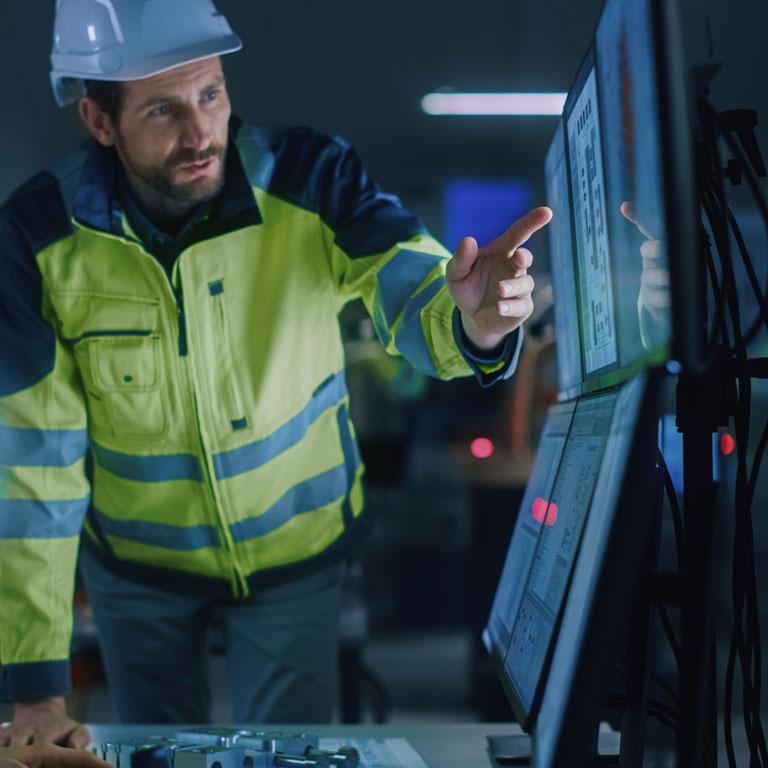
One possible scenario of using AI for production-related matters is the real-time forecasting of production quality. Based on the estimates thus obtained, machine operators are suggested specific measures to achieve the best possible production output. This applies, for example, with regard to temperature reduction of the machines in order to maintain continuous production quality. Forecasting thus provides an early warning system that enables the economical use of resources along with a considerable reduction in waste. During a teach-in period, the AI acquires knowledge which it subsequently uses to counteract reduced production quality caused by changes in machine parameters at an early stage. This method is called predictive control.
Keeping a handle on complex production-related matters
In a typical scenario where predictive control is applied, machine operators track production quality and key machine parameters via a user interface. In this scenario, the operator is not concerned with the quality of the volumes already produced, but monitors the expected quality of the volumes that will be produced during the next few minutes. Intelligent evaluation of sensor-based data from the machine enables reliable forecasting of output production quality. Production deficiencies can be addressed at an early stage through modification of machine parameters. It is, however, essential to also take into account the production costs. If there are several ways to achieve the desired quality, the most cost-efficient solution is always suggested. However, the authority to make the final decision always remains with the machine operator. He or she can accept or reject the AI's proposal for modification. And no matter how the human decides, the AI will always learn from this decision.
How companies and employees benefit from predictive control
The underlying technology helps to verify and optimize decisions made intuitively or based on manufacturing experience by using the data provided by AI. Valuable expert knowledge is made generally accessible in this way. At the same time, the workload of the employees is reduced. The decision-oriented visualization of the user interface helps machine operators to immediately understand the given situation thus enabling them to react quickly and to control several machines in parallel. For extended production lines, predictive control allows existing knowledge to be transferred to the new environment. As a result, optimized production is ensured from the very beginning.
Facing the future with confidence
Digitization of production expertise coupled with many years of experience makes companies less dependent on individual employees. In this way, the company can still continue to draw on the knowledge of its employees, such as machine operators, for example, even after their retirement. Experience that would otherwise be lost literally lives on in the algorithms. In this scenario, using AI comes with a considerable advantage, especially when it comes to international corporations. These struggle with the fact that despite almost identical framework conditions, the same level of quality cannot be achieved for production at different locations. Predictive control ensures that knowledge gained in production is aligned and maintained at a consistently high level throughout the world. New employees can thus be trained more quickly, and specialist knowledge is made accessible throughout the company. Digitization contributes to ensuring a future-proof environment, for example when it comes to coping with the continuously increasing shortage of skilled professionals.
Why is this technology only coming now?
The necessary framework conditions to enable predictive control have not been established until now. It requires a lot of high-performance computing resources to train the AI and mathematically optimize the production processes – not to mention the considerable memory requirements. Furthermore, there is an additional challenge associated with the interlinking of sensors, machines and systems in order to generate the necessary data and empirical values. These possibilities have just emerged in industrial companies in recent years as a result of the digitalization of production.
Keywords
More similar blogposts:
Found what you were looking for?
Start your intelligent search now