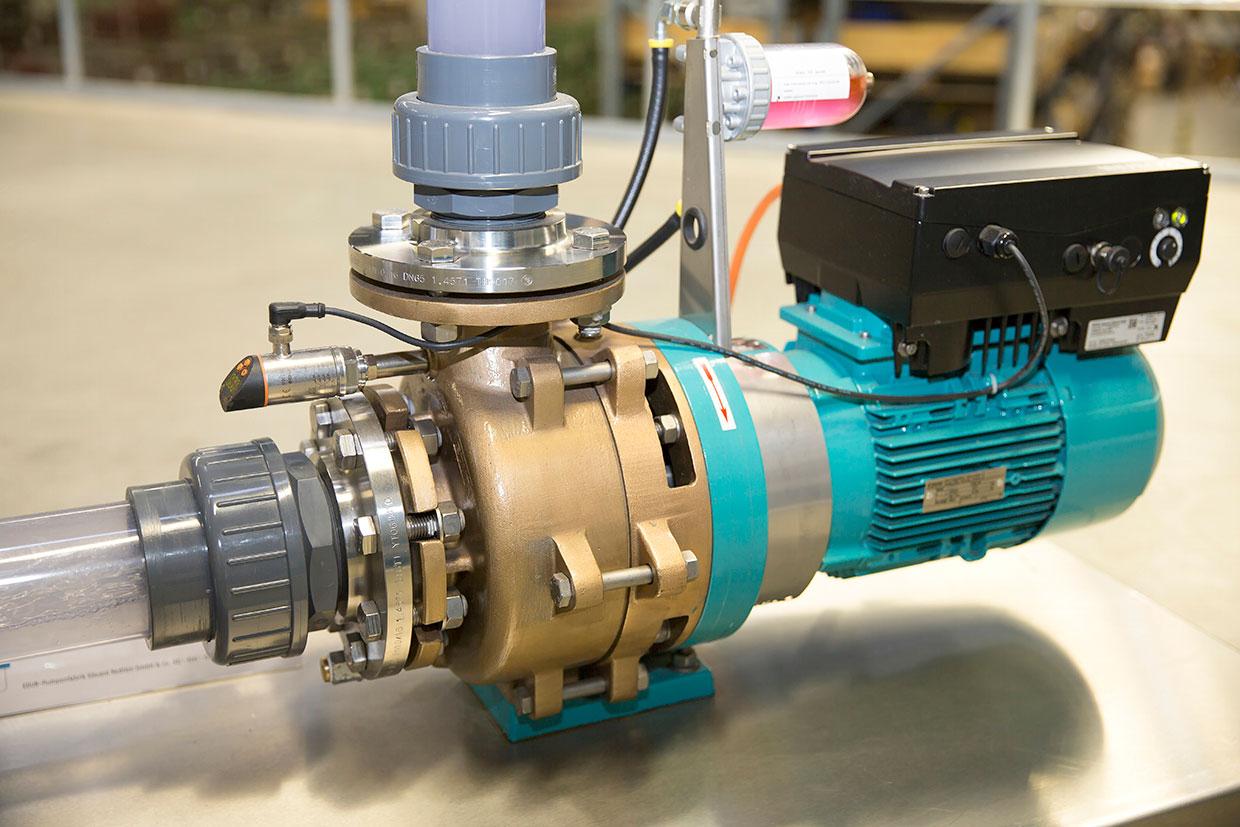
EDUR-Pumpenfabrik Eduard Redlien GmbH & Co. KG
When Eduard Redlien launched his first self-developed rotary pump in 1927, he was only 25 years old. In the start-up scene there was almost something like a gold rush atmosphere. His first self-priming rotary pump proved to be so robust and reliable that Redlien quickly expanded its customer base. Fist he expanded regionally, then later nationally and internationally. In the middle of the 80s came the successful shift from the serial manufacturing to discrete manufacturing for special customer requirements.
The right pump for every scenario
EDUR-Pumpenfabrik Eduard Redlien GmbH & Co. KG is a specialist for liquid and multi-phase pumps with a worldwide reputation. "With our products, customers do not think about how to integrate pumps into the existing infrastructure. We think about what kind of pump would fit perfectly into that infrastructure," explains Thomas Stegen, Head of IT Management/System Administration at EDUR-Pumpenfabrik. To ensure that delivery times and the price levels are still at a customer-friendly level, EDUR manufactures according to a modular principle. "That means we can usually deliver within five days," says Stegen. EDUR pumps are used in process engineering, in the energy sector for water supply and in shipping. Its customers range from small to large listed international machine and plant builders. The product range comprises around 20,000 pumps with a flow rate of up to 500 m³ / h and a discharge pressure of 40 bar. Sales and service are run through a worldwide network of partners.
Version change as an opportunity for the future
In terms of enterprise software, EDUR has been using the Microsoft Dynamics NAV ERP system for more than 20 years. When the support for the existing program version ran out, the company faced a challenge: an update to the current program version was unavoidable, but not easy to implement. In order to ensure their very short production times, the proportion of adaptations of individual processes and programs was high.
The upcoming version change was therefore a good opportunity to move existing structures closer to the standard. But there was a problem: Most production systems are based on a product configurator. Via predefined rules and in several steps this produces the appropriate variant. "In our case, the great variety of customer requirements could not easily be reconciled with the multitude of different product variants. The rules required for a product configurator would have been too complex," Thomas Stegen recalls, "So we started looking for a partner to harmonize our workflows with the software standard."
Industry know-how is crucial
That was easy to find at COSMO CONSULT. The size and the expertise of the software company in the production environment played an important role in the selection process. The specialists have their own certified industry solution in their portfolio in the form of the Configure-to-order solution. "At the workshops in the run-up to the awarding of the contract, we agreed with the consultants to adapt the operational requirements to the standard as far as possible. It was important for us to be sure that our partner could also provide the necessary manpower during the intense project phases", said the IT manager.
Transparent production processes
The project team needed just a three-year period for implementation and migration. In the area of production, it was possible to build the complex project identification on a multi-stage article structure. Since then, checklists have helped to find the right entry into the product structure. Today, the entire planning process for production and requirements runs in Microsoft Dynamics NAV - and with very high productivity. "In only a few cases do orders require informal communication. Most of them are fully automated. Our goal is to optimize the processes to such an extent that we separate the planning processes from the standard business in advance," explains Stegen. An important step has already been taken: All production information is managed centrally and is thus more easily accessible. This makes it possible to transfer all the information required for the production to the workplace after being tailored to the respective production order - from work safety information to concrete production drawings.
Currently, some 50 workstations are equipped with Microsoft Dynamics NAV. Most of them are in areas such as administration, sales, construction and service. In manufacturing, the IT manager is focusing on a different strategy: "Here we prefer mobile terminals instead of traditional PC workstations. That allows our employees to access relevant information from the ERP system from anywhere.” A quick scan of the machine engraving or the sticker is enough to get information on the production status or the next steps. "We save a lot of paper and distribute information much more efficiently. This considerably reduces the costs and effort required for communication, coordination and administration," adds Stegen.
Benefiting from high data quality
Asked about the further advantages of the new program version, the IT leader points to the improved data structure. Above all, production has gained in flexibility. If errors are discovered or if specifications are changed by customers subsequently, the required change management can now be done much more easily. Another area that benefits from the version change is customer service. "Now we have our customer data always readily available. We can research every process down to the smallest detail. If a customer calls, up to 80 percent of our employees are immediately ready to provide information - even if the call does not concern their specialist area. For us and for our customers, this is a tremendously great added value," said Stegen.
The future speaks “Industry 4.0”
At the moment, EDUR is striving for predictive maintenance of its pumps. These are to be provided with a QR tag, which can be used by service technicians on site to access information on running time, maintenance history and the parts in use via smartphone. In addition, data from vibration sensors on the pump can be combined with statistically calculated failure probabilities. This allows maintenance intervals to be optimized and maintenance work outside regular schedules or even failures to be largely avoided. "In this way, we can significantly increase the already high reliability of our pumps. With Big Data and Industry 4.0, as the current trend of automation and data exchange in manufacturing technologies is known in Germany, we now have the chance to realize such scenarios,” says Thomas Stegen. From his point of view, in the future it will be crucial to optimize communication with customers on the basis of well-structured information without deviating too far from the standard of the ERP basis.
More COSMO References
Be part of our COSMOs
Expand your COSMOs and register in our customer portal for exclusive benefits & services
#myCOSMO
Found what you were looking for?
Start your intelligent search now