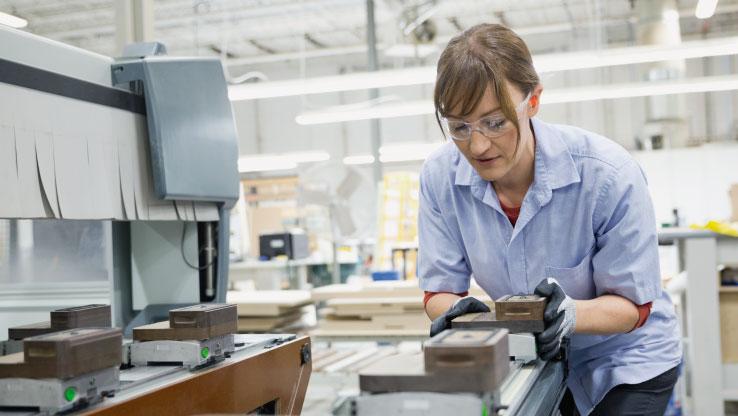
Hoy en día, los sistemas ERP de Planificación de Recursos Empresariales, son omnipresentes en las grandes empresas, y la tendencia es adaptarlos para ponerlos al alcance de las PYMES. Para los principales analistas, el crecimiento y éxito de la adopción de ERPs en el nuevo milenio dependerá de la capacidad de los antiguos ERPs para ampliar su alcance al Customer Relationship Management (CRM), Supply Chain Management (SCM), la Inteligencia Artificial y otras.
La Planificación de Recursos Empresariales cubre las técnicas y conceptos empleados para la gestión integrada de negocios como un todo, desde el punto de vista de la gestión efectiva de recursos para mejorar la eficiencia de una empresa.
La evolución de los ERP
El Enterprise Resource Planning (ERP) ha evolucionado durante cuatro décadas hasta convertirse en una herramienta estratégica. Ha evolucionado gracias a las continuas mejoras realizadas al incorporar nuevas técnicas de gestión para la mejora de la eficiencia y también gracias a desarrollos e innovaciones en el campo de las TIC.
El MRP, paso previo a las soluciones ERP
Antes de 1960, las empresas solían usar técnicas tradicionales de gestión de inventarios. Las más utilizadas eran la Cantidad Económica de Pedido (EOQ) y la lista de materiales o BOM (Bill of Materials) pero eran unos sistemas limitados en alcance. Los sistemas ERP son una evolución de los Sistemas de Planificación de Materiales (MPS) de los 80. Hasta llegar allí pasaron varias fases de desarrollo.
Material Requirement Planning (MRP)
El MRP fue el concepto básico de gestión y control de la producción a mediados de los 70, y se considera el primer paso en la evolución de los ERP. Las operaciones de ensamblaje con miles de piezas como la fabricación de automóviles habían llevado a enormes inventarios. La necesidad de reducir los altos niveles de inventario llevó a los primeros sistemas MRP para planificar el lanzamiento de órdenes. Lanzar las órdenes de forma planificada garantizaba una planificación por fases adecuada de los subcomponentes, teniendo en cuenta las complejas relaciones de componentes a montar caracterizados por la Lista de Materiales. Veamos un ejemplo:
Un ejemplo clásico, utilizado en muchas de las demostraciones de los primeros ERPs por su simplicidad, es la fabricación de una bicicleta. Para fabricar 100 bicicletas, se necesitan 200 ruedas, 100 pedales y varios cientos de radios. En una fecha dada, una planta puede tener 40 bicicletas acabadas en stock, 57 ruedas, 43 pedales y 879 radios. Si la planta va a montar 20 bicicletas en los siguientes 4 días de producción, las ruedas y los radios no son un problema trivial. Si se quiere tener en cuenta la demanda independiente de las piezas, es fácil visualizar la complejidad.
Una planta de fabricación de automóviles, con cientos o miles de piezas, debe enfrentarse a problemas de una magnitud mucho mayor. Los sistemas MRP usan la capacidad de computación de los ordenadores para gestionar las bases de datos con los plazos de entrega y cantidades de los pedidos, y correr los algoritmos para implementar la explosión de las BOM. Los sistemas MRP pusieron orden en el complejo proceso de planificación de materiales en una planta de fabricación discreta.
En esencia, el MRP se dirige a una única tarea en la fabricación, la Planificación de Necesidades de Material (Material Requirements Planning). Se adoptó para la creación y mantenimiento de datos maestros y Listas de Materiales (BOM) de todos los productos y componentes de una empresa. EL MRP era una consecuencia del procesamiento de las BOM, con una gestión de órdenes de compra que utiliza la gestión de listas de componentes y su fabricación o compra (aprovisionamiento).
Planificación de Recursos de Fabricación
La evolución natural de la primera generación de sistemas MRP fueron los sistemas de planificación de la producción MRP II, orientados a la función completa de manufactura en lugar de a una única tarea dentro de la fabricación.
EL MRP II iba más allá del cálculo de necesidades de material para tener en cuenta también la carga y la programación. Los sistemas MRP II podían determinar si un programa de producción determinado era factible, no solo desde el punto de vista de la disponibilidad de material, sino también desde el punto de vista de otros recursos.
Los recursos contemplados por el MRP II eran las plantas de producción, la capacidad de las máquinas y las secuencias de fabricación que precedían al programa. Las nuevas funciones permitían a los sistemas MRP II hacer funcionar el sistema en bucle. Primero se utilizaron para chequear la viabilidad de un plan de producción teniendo en cuenta las restricciones, en segundo lugar, para ajustar la carga de los recursos, si era posible cumplir con la planificación de la producción, y, en tercer lugar, planificar los materiales usando los sistemas MRP II tradicionales. Tanto los sistemas MRP como los MRP II tuvieron bastante éxito en la industria. Dada la potencia de los sistemas y bases de datos, los algoritmos y su integración, las organizaciones encontraron en los años 80 un soporte real para gestionar eficazmente sus operaciones de fabricación.
Enterprise Resource Planning (ERP)
Los años noventa trajeron una competencia global sin precedentes, enfoque al cliente y ciclos de producto cada vez más cortos. Para responder a las nuevas demandas, las corporaciones tuvieron que moverse hacia una fabricación ágil de productos, con continuas mejoras y reingeniería de procesos. Esto exigía integrar la fabricación con otras áreas funcionales, como contabilidad, marketing, finanzas o RRHH.
El cálculo de costo de actividades (Activity-based costing) no sería posible sin la integración de la producción con la contabilidad. La personalización masiva de la fabricación necesitaba la integración de marketing y producción. También se hizo necesaria la integración con RRHH para la fabricación flexible. En resumen, en los 90 se hizo necesario integrar toda la gestión, y surgieron los ERPs como concepto.
ERP Extendido (E-ERP)
La evolución del concepto de ERP, de la Planificación de Necesidades Empresariales, llevó al “ERP extendido” (e-ERP) o ERP capacitado para web. Con la globalización por un lado y el desarrollo masivo de la tecnología de Internet por otro, surgió la necesidad de soluciones IT basadas en la web.
Enterprise Resource Planning II (ERP II)
El ERP II va un paso más allá del e-ERP, para incluir capacidades como la gestión de relaciones con clientes (CRM) la gestión del conocimiento, los flujos de trabajo automatizados y los recursos humanos, todo en un entorno web que facilita la gestión de organizaciones distribuidas geográficamente.
Los ERP y la fabricación discreta
Los sistemas ERP actuales son una evolución de los MRP y MRP II. Los MRP iban dirigidos a la única tarea de planificación de materiales. Los MRP II ampliaron el alcance a toda la fabricación. La industria manufacturera tradicionalmente ha acogido bien el uso de ordenadores. En parte, porque en el sector abundan los ingenieros, que no suelen tener fobia a las TI. También el uso de soluciones CAD/CAM han preparado a la industria para la tecnología. De hecho, los ingenieros industriales han contribuido mucho a la computación con sus contribuciones en gráficos, geometría, visualización, etc.
De hecho, grandes corporaciones como Hewlett Packard (HP) o Digital se veían a sí mismas como empresas manufactureras hasta los 80. Los sistemas MRP complejos se consideraban lo último en sistemas de información empresarial. Las inversiones en hardware y software para gestionar soluciones para producción complejas dieron a estos sistemas una visibilidad sin parangón en la industria. En comparación, los sistemas de contabilidad, financieros o de RRHH eran de una importancia menor.
El paso siguiente, con la globalización de las operaciones, fue extender los sistemas de información a lo largo de la cadena de suministro, lo que implicó complejas integraciones de hardware y software. De forma parecida fue necesario integrar las redes de fabricantes con distribuidores, ya que para reducir los ciclos de vida de los productos eran precisos sistemas de fabricación de respuesta rápida.
La globalización demandó también integrar las finanzas, cumplir con acuerdos y cuotas comerciales y manejar múltiples divisas y normativas, periodos y códigos contables.
De golpe, lo que se hizo necesario fueron sistemas de información empresarial más allá de la fabricación, que gestionasen logística, materiales, producción, proyectos, calidad, finanzas, ventas y recursos humanos. Surgieron sistemas especializados en gestión de clientes (CRM) de la cadena de suministro (SCM) de la gestión de almacenes (WMS) y así ad infinitum, prácticamente. Pero… se volvió casi imposible integrar módulos individuales para cada función y quedó claro que la integración debía venir desde el momento del diseño. Todo y así, los sistemas ERP se convirtieron en la elección natural para gestionar íntegramente una empresa.
Los ERP han evolucionado
Los tiempos han cambiado. Y mucho. Desde hace muchos años hemos oído una y otra vez que “un ERP en la nube era imposible”, por ejemplo. Ahora no es que sea realidad, es que es casi el estándar. Las soluciones Microsoft Dynamics, por citar un ejemplo de primera línea, aúnan funciones ERP y CRM en la nube, y están especialmente adaptadas a las necesidades y posibilidades de las PYMEs. Si está sopesando iniciar la Transformación Digital de su empresa, estas son sus herramientas, y COSMO CONSULT un Partner idóneo para ella.
Más entradas de blog similares:
¿Ha encontrado lo que buscaba?
Inicie ya su búsqueda inteligente